Japanese Paper - washi
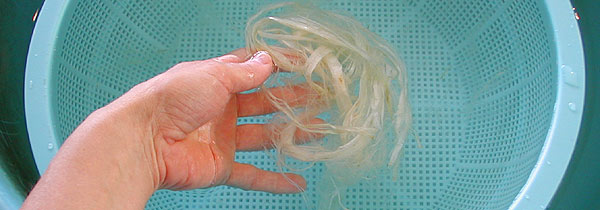
For creating Japanese woodblock prints, the handmade paper,
called washi, is indispensable. Its peculiarity lays
in the use of bast with long fibres und a special papermaking
technique, nagashi-zuki, which is unique in the world.
In opposite to Western woodblock printing, where a layer of oil-based ink is
printed on top of the paper, during Japanese woodblock printing the water-based
ink is pressed deeply into the paper. The very absorbent and strong Japanese
paper is able to absorb the ink evenly and to resist the often repeated printing
without loosing its shape.
Handmade paper has a long tradition in Japan and was used over
the centuries for the most different purposes. Paper was used as letter paper,
for calligraphy, woodblock prints, books and as wrapping paper, but also lamps
and umbrellas were made from it, and sliding doors were pasted with it. Paper
was used for weaving clothes and ropes, and for making waterproof raincoats.
Shaped and lacquered it was used for making boxes. Because of his lightness
and strength it was used for fireworks and of course as toilet paper.
Washi had and has also much meaning in the spiritual life, f. e. at sacred
places of the shinto religion.
History
The history of paper starts in China. The court
official Ts'ai Lung is regarded as the inventor of paper, as he presented his
paper in the year 105 A. D. to emperor Ho Ti. This paper was actually an improvement
of former papers, made from the barks of mulberry trees, hemp, old fisher nets
and rags. After this presentation, paper soon got very popular and replaced
bamboo strips and partly the expensive silk as mediums for writing.
In the year 610 paper came to Japan, where it was presented to empress Suiko
by the Korean Buddhist monk and craftsman Danchó. One of Suikos princes,
Shotoku, improved this paper and initiated the plantation of kozo
trees, which are a kind of mulberry tree.
In the Nara period (710-784) with its rich cultural life, paper
already had much meaning. One of the first printed texts of the world is dated
in this period: the dharani, which were ordered from
empress Shotoku. These were Buddhist verses, which were printed until 770, each
stored in a small wooden pagoda. The papers used for that were mostly from kozo
and hemp. Many papers were dyed or created in special ways, which shows that
papermaking of that time had achieved already big progress. During the Nara
and the following Heian period, copying of Buddhist sutras was very popular
under aristocrats and the need for paper grew rapidly. The general population
however had hardly access to paper.
In the Heian period (795-1185) the number of paper producing
provinces grew from nine to forty. During the regency of emperor Keijo (806-9)
the court initiated a perfectly equipped paper mill, the kanya-in
on the Kanya river at Kyoto, which produced every year 20 000 sheets of the
size 60 x 36 cm exclusively for the courts consumption. The decline of the court
power had an effect also onto its paper mill. The papermakers, who had lived
a slave-like life until then, mixed with the civil population and passed on
their knowledge. More and more private papermaking studios
emerged. Beside hemp and kozo, also the wild growing bush gampi
was used.
In the Japanese middle age, the Samurai period (1192-1603),
the power moved from the emperors court to the samurai. The conditions got more
democratic and so the situation for trading improved. Due to that and the huge
need for paper, papermaking made big progress.
There was paper for many different purposes like the popular mino-gami from
Mino, which was used in the Edo period for all official documents. Papers from
Tosa and Suo were used for the daily needs. The thin and soft yoshino-gami
was used as toilet paper and for filtration.
Paper now was mainly made from farmers during the winter time for an extra income.
Normally a papermaking family had a studio with one or two vats, some papermaking
villages however had bigger studios with up to 20 and more vats.
During the Edo period (1603-1868), when Japan was closing herself
from the out world, the daimyos (sovereigns) were maintaining paper mills for
their own consumption and for giving the paper as tribute to
the shogun. The papermakers guaranteed for the papers quality with their and
their families lives.
The most popular paper of that time was the hanshi, which was used for
books, notebooks, umbrellas and sliding doors and which's size was 25 x 35 cm.
From hosokawa documents and maps were made. The santome was used
for wrapping clothes. Winter clothes were made from thick paper like the senka
from Iyo, while ceremony clothes and mosquito nets were made from shifu
. An important aspect was now the use of paper for the woodblock prints
with water-based inks. Thousands of editions were printed and sold for little
money.
After Japans opening in the 1860th, the government of the Meiji
emperor initiated a new industrial development to stand even with the Western
countries. This resulted in an increasing need for paper, so that the mechanical
production of paper was introduced in Japan. While the demand for handmade paper
was decreasing, the papermaking craft however stayed alive.
In the end of world war two the Japanese papermakers were involved in a military
project: about 10 000 paper balloons were built to fly with bombs to the USA.
But not many of these balloons arrived and not much damage was done.
Today the paper lost its meaning in many of the traditional areas. For the huge
demand of writing and printing, paper is produced after the Western method and
many things like umbrells and lamps now are produced by using cheaper materials.
The craft of papermaking has also changed: different from former times, when
paper was made only during the winter which was better for producing high quality
paper, papermaking nowadays is done during all year. Some of the natural materials
were substituted with chemicals and machines are used now. There are much less
papermaking studios today and the knowledge about papermaking is not as common
as it once was. The demand for handmade paper however is big: washi is
still used as letter paper, for calligraphy, notebooks, business cards etc.
It also is the perfect paper for Japanese woodblock printmaking and is widely
used for artistic purposes.
Technique
In old times papermaking was done during the winter season.
It was a side business of farmers, who were living in the mountains and didn't
have much land for rice farming but a lot of clear water from the rivers. These
papermakers were doing all the process from cutting the trees to the actual
papermaking. The season began in November after harvesting the rice and ended
in April or May with the rice planting. The winter cold also was an advantage
for making paper by naturally conserving materials. Today paper is done through
all year.
Material
The traditional plants which's fibres were used for papermaking
are the kozo tree ( mainly used today) and the bushes gampi and
mitsumata. Here I am referring to the use of the wild growing kozo
(Broussonentia Kajinoki), which is a member of the mulberry tree family.
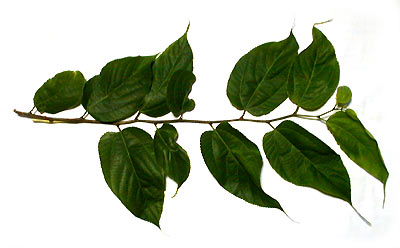
Harvest
The branches of the kozo are cut in November after the
leafs fell down. They are cut shortly over the trunk and put in bundles of same
length.
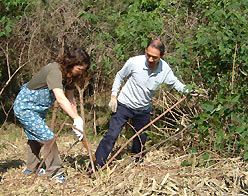
Steaming the branches and removing the bark
Only the inner white bark is used for papermaking. The bark
therefore has to be removed from the branch's wooden part. To make this easy,
the branch bundles are steamed for one or two hours. This takes part in an airproof
barrel or box over a cauldron with hot water. After the steaming, the barks
are soft and can be pulled off very easily.
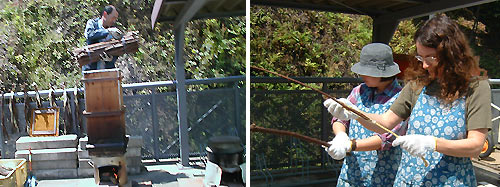
The steaming and removing of the bark was a popular work, which
was often done in team work of villagers of all ages and both sexes. In this
state the bark is called kuro kawa, black bark. It now could be dried
and stored for later need.
Removing the outer barks
Afterwards the outer black bark and the green bark underneath
are removed with a sharp knife, together with spots or damages in the bark.
The remaining inner bark is white and called shiro kawa. Only this is
used for making fine paper.
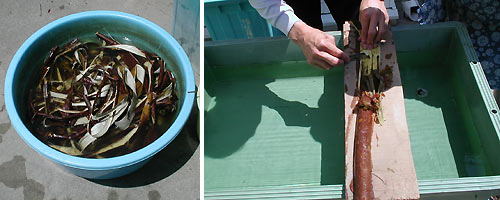
Cooking the white barks
The cooking and washing of the barks has big influence on the
paper, depending on the cooking time and the dosage of the used chemicals. The
barks are cooked in an alkaline solution to remove all parts, except the cellulose
fibre, like pectin, wax and rubber. Traditionally potash was used while today
this is also done with soda ash. After the cooking the water is brown and the
barks are washed. Traditionally this is done in a bamboo basket in a river.
The fibres can be pulled apart now very easily.
Bleaching the white bark
Paper made from this bark is not white but has a yellow tone.
For a whiter paper the barks have to be bleached, what was done in old days
in the river by fixing the barks with stones in the river bed or by exposing
the barks to sunlight in the snow. Today mainly chemicals are used for bleaching.
Removing specks
The barks now have a silk-like appearance. They are ready for
removing specks, dust etc. This work, called chiri-tori, is exhausting
and mainly done by middle-aged women. While the barks are floating in the running
water of a river or in a bowl, the specks are removed with the fingers. For
producing high quality paper the process is done repeatedly. Afterards the pieces
are pressed into ball shape.
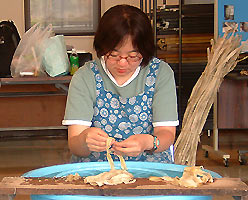
Beating
These balls are put onto a board from hard wood or stone and
beaten with rods or hammers from hard wood. This way the fibres are pulled apart
without getting destroyed. This work was traditionally done by women at night
time, so that the material was ready in the morning for the papermaking. During
the beating the women sang special beating songs. Today machines are doing that
work without singing.
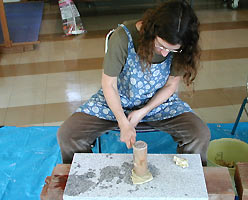
Papermaking
For making the paper the fibre pulp is put into a vat with water
and mixed perfectly with it, so the fibres are floating evenly in the water.
Especially for the later described technique nagashi-zuki,
a mucilage substance is added, called neri, which is extracted from the
roots of the plant tororo-aoi (Hibiscus Manihot L.). Neri is a
very important part of the Japanese papermaking as it makes the fibres float
evenly and prevents them from sinking down. Also it makes the pulp run more
slowly through the mould during the papermaking and so allows more control over
the process. Today neri is also available in synthetic form.
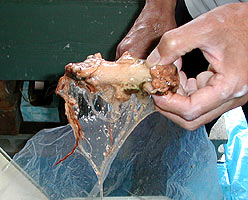
There are two methods of Japanese papermaking. The one is called
tame-zuki and resembles the Western method. The mould is shortly
dipped into the vat and then moved vertically and horizontally until the water
has run down and a layer of clinging paper fibres remains. This paper layer
is pressed onto a pile, while the single sheets are separated from each other
with cloth.
The second method, which is typical for Japan and unique in
the world, is called nagashi-zuki. The mould which is used here
consists of an outer frame, the keta, which is holding a movable bamboo
screen, the su.
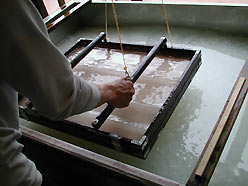  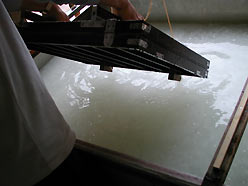
The papermaking starts with the so called kesho-mizu:
dipping the mould just shortly into the pulp and pouring out the excess water
immediately. This way the mould gets covered with a thin layer of fibres. This
results in a smooth paper surface and prevents the paper sheets from later sticking
together.
Afterwards the actual papermaking is done by dipping again and sending the pulp
over the screen with vertical and horizontal movements. Before the water has
completely run down, the rest is poured out, this way removing bigger fibre
parts or knots. This process can be repeated until the paper has reached the
desired thickness. The frame then is opened and the inner screen removed. It
is raised over the papermakers head and let down onto the pile with the already
formed sheets. By pouring water over the screens front edge, the paper layer
separates from the screen.
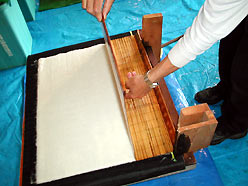
Pressing the paper
The freshly formed paper is very wet and cannot be dried in
this state. Therefore it has to be pressed which requires a lot of skill and
experience. The power in pressing the paper can influence the result. Traditionally
the papers were pressed by charging the paper with heavy beams or in screw presses.
Today hydraulic presses are used. The pressure has to increased very slowly
to prevent the paper from being damaged.
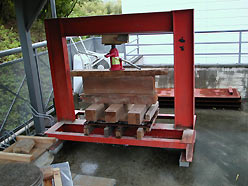
Drying the paper
After the pressing the paper is ready for drying. Traditionally
the papers are brushed onto pine wood boards with a horse hair brush. Additionally
the edges of the papers are pushed onto the board with a wet camellia leaf.
The boards then are exposed to the sun. Today papers are dried on hot plates
too.
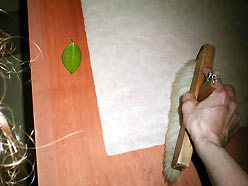  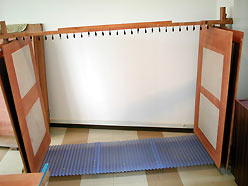
Last steps
When the papers are dry, they are taken from the boards and
roughly divided into classes of different quality. Before being sold they again
are checked. Every paper has to have a certain colour and thickness and has
to be free von spots. Some papers also are cut to remove the deckle edge. The
finished paper of course makes the papermakers heart feel very happy.
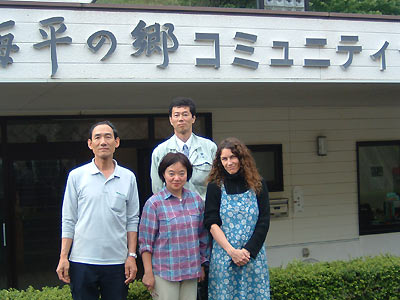
I want to thank my teacher Okuda Yoshiharu (left), Kosaka Masahiro
(middle), the City of Tsuna and all the other people who were involved.
Bibliography
Barrett, Timothy: "Japanese Papermaking: Traditions, Tools,
and Techniques”, New York & Tokyo: Weatherhill, 1983
Hunter, Dard: "Papermaking – The History and Technique
of an Ancient Craft”; Knopf, New York, 1943 and 1978
Jugaku, Bunsho: “Paper-making by hand in Japan”,
Meiji-Shobo Publishers, Tokyo, 1959
Narita, Kiyofusa: “Japanese papermaking”, Hokuseido
Press, Tokyo, 1954
Back to top
 |